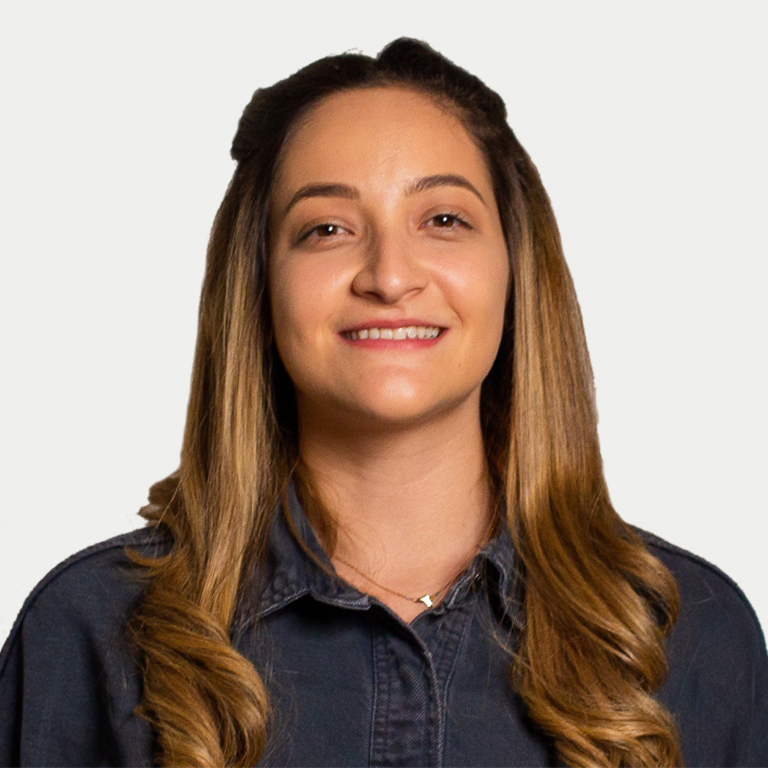
Natali Walton Chacin
Analyst Risk Engineer
-
United Kingdom
The 2022-2023 period was defined by a number of factors that challenged the energy and power industry as well as the global economy. Recovery from the Covid-19 pandemic was further complicated as the spotlight on energy security intensified as a result of the Russia-Ukraine war, soaring energy and commodity prices contributed to inflationary pressures and tightening of fiscal policies, and supply chain constraints impacted most industries. At the same time, the global groundswell of social and political commitments to address climate change and adopt sustainability measures renewed the urgency to transition to clean energy sources. Despite the macro-economic landscape, the current volume and scale of investment in the energy and power industry is unprecedented. The terms energy security and energy transition have become the part of our common language and serve as reminders of how essential the industry is to both developed and emerging economies.
The past two editions of this report have highlighted the dynamic factors that can affect the operating conditions and risk landscape for the industry. The 2020 report reflected the aftermath of the active loss period of 2017-2019, while the 2022 report captured the uncertainty, heightened risk considerations, and reduced operational activity through the Covid-19 pandemic. The past two years have been a mix: there was more loss activity in 2022, though this subsided in 2023, particularly in relation to onshore assets.
Since our last report, only two incidents have resulted in property damage losses in excess of US$240 million, which is the adjusted threshold for the 100 highest value losses. In researching this edition, we have also revisited historical losses where additional information is now available that may not have been at the time of our previous report publication. Using updated investigation reports and data from insurance markets, we have identified twelve incidents that now qualify for the top 100 ranking.
Date | Location | Cause | Sector | Ranking |
1974 | Norway | Mechanical failure | Upstream | 65 |
1982 | Canada | Mechanical failure | Upstream | 84 |
1987 | US | Fire and explosion | Upstream | 18 |
1991 | Norway | Mechanical failure | Upstream | 31 |
1999 | Angola | Mechanical failure | Upstream | 59 |
2003 | Norway | Mechanical failure | Upstream | 35 |
2007 | Canada | Fire | Refining | 78 |
2009 | South China Sea | Natural catastrophe | Upstream | 87 |
2013 | Kazakhstan | Mechanical failure | Upstream | 21 |
2014 | Netherlands | Explosion | Petrochemicals | 53 |
2015 | US | Mechanical failure | Upstream | 27 |
2017 | Canada | Fire | Refining | 99 |
Marsh engineers have also analyzed a number of incidents that did not rank in the top 100 but are notable to insurance markets because the combined value of property damage and business interruption claims for each loss was significant. Many of these incidents are still under investigation to determine the cause of the loss, and will undoubtedly provide valuable learnings for energy operators.
In the 2022 report, one of the major risk factors identified was the potential downsizing of operations and loss of experienced staff as organizations focused on recovering from the Covid-19 downturn. While the energy industry demonstrated exceptional resilience and innovation to overcome the challenges during the lockdown period, there have been a number of recent incidents that may indicate a loss of operational discipline. The examples below are not in the top 100 dataset but demonstrate the importance of embedding robust operational processes and ensuring personnel are appropriately trained.
A fire occurred when the wrong item of equipment was opened for maintenance. The incident resulted from poor shift handover and maintenance practices.
A LNG line ruptured when left blocked for an extended period without a thermal relief path. Investigation identified inadequate procedures, procedures not followed, high overtime rates leading to operator fatigue, and poor alarm management.
A fire occurred when a light naphtha stream was drained to the refinery oily water system, creating a vapour cloud which ignited. One of the factors leading to the incident was an inadequate response to an abnormal situation.
Two key factors are increasingly influencing the need to review indemnity periods for business interruption coverage: the intervention of local regulators, and an upswing in global construction activity. Both of these issues have the potential to delay the restart or prolong the rebuild of plant following an incident.
Regulators are becoming more involved in the aftermath of major incidents at operating sites, particularly those involving serious injuries or fatalities. Notable incidents that have triggered significant regulatory interventions include an explosion at a LNG facility in Texas, US (2022), a fire at a refinery in France (2019), an explosion at a refinery in Germany (2018), and an explosion at a refinery in Wisconsin, US (2018).
Regulatory interventions can introduce various implications including:
Construction activity ramped up post the Covid-19 restrictions but the backlog of projects coupled with high inflation has led to higher costs and longer lead times.
Construction cost indices in the ten-year period from 2010 to 2020 recorded average annual increases of 1% to 2.0%. However, prices started to spike from late 2021 as the world emerged from lockdowns and in 2022 alone, many indices recorded double-digit increases.
Data source: US Bureau of Labor Statistics
Index base adjusted, January 2013 = 100
Although the rate of increase has decreased in the last year, overall construction costs are still at significantly higher levels. For example, steel prices are at or close to a 10 year high.
Data source: WSJ Online
Increasing construction costs, supply chain constraints, as well as labor and material shortages highlight the importance of carefully evaluating policy indemnity periods and conducting comprehensive reassessments of plant rebuild values to align with prevailing economic conditions.
The scale of investment in energy projects is creating competition for talent as companies strive to secure resources to manage existing operations and new strategic initiatives. The competition for skilled personnel and the migration of talent between industries may pose tangible risks for energy operators. Companies must find ways to manage workforce turnover while maintaining knowledge, competence, and operational excellence to mitigate the inherent hazards involved in building and operating energy assets.
Existing energy operators may have a robust safety culture, but ensuring regular reviews of operationally critical processes and procedures is essential. Similarly, new operators should be mindful that building culture and expertise will take time. Operators can improve their chances of preventing significant and avoidable losses by using benchmarking studies, implementing comprehensive training and development programs, ensuring consistent maintenance practices, and regularly testing risk management and response plans.
The reality of climate change means companies have to rethink their infrastructure needs and design. Increasing variability in weather conditions and more frequent natural catastrophe hazards increase the risk exposure of most energy facilities. Operators are challenged with improving the resilience of existing operations today, and elevating climate considerations into expansions or investments. Furthermore, with the increasing scrutiny of environmental, social, and governance policies, future insurance market capacity and risk transfer mechanisms for traditional energy facilities may narrow.
Cyber risks are escalating with the digitalization of energy systems. A cyberattack on operational technology (OT) such as SCADA applications could paralyze production or power generation. But even the operational management of change associated with OT deployment needs careful planning, process management, and implementation to prevent significant business interruption losses and workforce risk.
Regional conflicts increase the risk of energy infrastructure been strategically targeted. Aside from increased insurance costs, operators need to be aware of war and other exclusion clauses that may affect insurance coverage.
Analyst Risk Engineer
United Kingdom
SVP Risk Engineering Hub Leader
United Kingdom