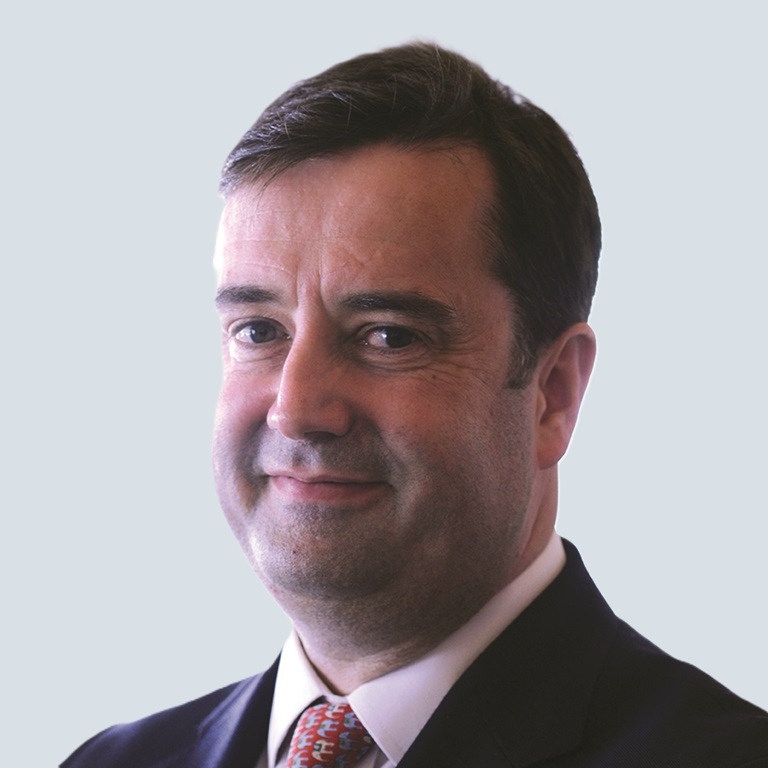
Andrew George
-
United Kingdom
The report includes details of the costliest incidents in the energy industry, and is an opportunity to revisit lessons from the past. It allows us to look back at the industry’s history, identify key issues and trends from large losses, and understand whether the industry is making progress on improving operations and risk management practices.
By reflecting and learning from the past, and continually reviewing and challenging our notions of best practice, we can build the resilience that the whole industry wants, and needs, to achieve.
100 largest losses in the hydrocarbon industry - 2022
United Kingdom
United Arab Emirates
United Arab Emirates